(1)脱H2O
脱H2O是因为导气管中如果积累了水会溶解H2S腐蚀管道,此外当沼气被加压储存时,沼气中的水会凝结冻坏储气罐。发酵装置出来的沼气中所含的水分形式是饱和水蒸气,一般采用冷分离法将其除去。通过调整压力引起混合气体温度发生变化,使水蒸气从气态冷凝为液态的水后,将其从沼气中脱除。此法经济简单,被大多数沼气工程所采用。
沼气冷却的方式有自然降温及机械脱水两种。冷却温度还要考虑下一步脱硫过程中不同脱硫剂对水分量的要求,根据脱硫剂的水分合理量进行适当的初步冷却。
在沼气输送过程中,还有一部分水要析出。为了避免析出的水分腐蚀或堵塞管道,常在管路的低处安装集水器,定期排除集水器中的水。
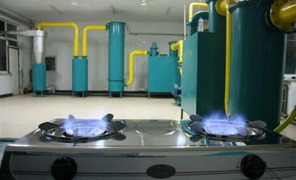
(1) H2O removal
H2O removal is due to the fact that H2S will dissolve and corrode the pipeline if water accumulates in the air duct. In addition, when methane is stored under pressure, the water in the methane will condense and freeze the air storage tank. The form of moisture contained in biogas from fermentation unit is saturated steam, which is generally removed by cold separation method. The temperature of the mixed gas is changed by adjusting the pressure, so that water vapor is condensed into liquid water from a gaseous state and then removed from biogas. This method is economical and simple, and is adopted by most biogas projects.
There are two ways of methane cooling: natural cooling and mechanical dehydration. The cooling temperature should also consider the water content requirements of different desulfurizers in the next desulfurization process, and appropriate preliminary cooling should be carried out according to the reasonable water content of the desulfurizer.
In the process of biogas transportation, there is still some water to be separated out. In order to prevent the precipitated water from corroding or blocking the pipeline, a water collector is often installed at the lowest part of the pipeline, and the water in the water collector is regularly drained.
(2)脱H2S
脱H2S是为了避免H2S腐蚀设备、H2S中毒和如果沼气燃烧H2S被氧化成SO2或SO3造成更大的危害。
总结出来的8种H2S脱除方法可以分为物理提纯、化学净化和生物吸收。现就3种机理中常用的方法分析如下。
① 活性炭吸附工艺。在变压吸附系统中H2S可以通过用KI浸泡过的活性炭去除。此过程中,H2S被转化为单质S和H2O,单质S就被活性炭吸收了。在连续运行的情况下,系统要包含两个吸附装置。如果活性炭上H2S的浓度超过3ppm,需要进行再生。
② 氧化铁吸收工艺。通过氧化铁来吸收沼气中的H2S,此工艺的脱硫原理如下:
Fe2O3?H2O+H2→Fe2S3?H2O+3H2O
(1)此反应是放热反应,低温度要求12℃,佳反应温度为25℃~50℃。所以,实际工程运营中,需要加热来达到佳反应温度。另外,H2S的脱除是通过在活性氧化铁表面的水膜中离解成H+和S2+后,再进行化学反应。因为此反应需要一定量的水,一般要将脱硫剂的水分含量控制在10%~15%。所以沼气在前面的脱水过程中温度不能太低,水分不能脱除得太多,但也应避免生成的冷凝水使球状氧化铁粘在一起,减少了反应表面,从而影响脱硫效果。
此法的脱硫工艺中产生的硫化铁可以被空气氧化再生,生成氧化铁和单质S。此工艺的反应原理如下,
Fe2S3?H2O+3/2O2→Fe2O3+3S+609kJ
(2)从反应式可以看出,再生过程中会放出大量的热,因此常常会发生自燃。为防硫剂自燃,一般需要对卸除的废脱硫剂喷洒少量水。另外,在经过很多次重复使用后,氧化铁的表面上会覆盖一层硫单质,所以就需要更换氧化铁。通常一个装置中要配有两个反应床,一个进行脱硫时,另一个可以进行再生。
在目前的畜禽养殖场沼气工程中,氧化铁吸收工艺被称为干法脱硫。另外有一种常用的湿法脱硫。湿法脱硫的脱硫剂多用浓度为2%~3%的碳酸钠溶液。此两方法的脱硫剂都可以再生。
③ 生物脱硫法。该法是利用无色硫细菌,如氧化硫硫杆菌、氧化亚铁硫杆菌等,在一定的温度、湿度和微氧的条件下,将H2S氧化成单质S或H2SO3。脱硫机理为:①H2S气体溶解,即由气相转化为液相;②溶解后的H2S被微生物吸收,转移微生物体内;③进入微生物细胞内的H2S作为营养物被微生物分解、转化和利用,从而达到去除H2S的目的。其反应方程式如下:
2H2S+3O2→2H2SO3
2H2S+ O2→2S+2H2O
大部分的硫氧化细菌都属于硫杆菌属。硫杆菌随处可见,用来脱除H2S并不需要接种。另外,大多硫杆菌是自养的,厌氧消化物的表面可以提供给它们一个生长所需的微观好氧环境和必需的营养。所以,运用生物法脱硫,直接往厌氧消化罐或储气罐中通入一定量的O2或空气并保持一定时间即可,方法比较简单。适当的温度、反应时间和空气量可以使沼气中的H2S含量减少50ppm。
在实际运用中,沼气中通入O2或空气的量根据沼气中H2S的含量确定,一般为2%~6%的空气。对于不同甲烷含量的沼气,空气中的爆炸范围不同,所以必需采取一定的措施避免沼气中通入过量的空气引起爆炸。同时,生物脱硫也存在过程不容易控制、脱除出来的单质S容易堵塞填料及损害曝气头等缺点。
(2) H2S removal
H2S removal is to avoid H2S corrosion of equipment, H2S poisoning and greater harm if H2S is oxidized to SO2 or SO3 during biogas combustion.
The eight H2S removal methods summarized can be divided into physical purification, chemical purification and biological absorption. Now, the methods commonly used in the three mechanisms are analyzed as follows.
(1) activated carbon adsorption process. H2S can be removed by activated carbon soaked with KI in pressure swing adsorption system. In this process, H2S is converted into elemental S and H2O, and elemental S is absorbed by activated carbon. Under the condition of continuous operation, the system should include two adsorption devices. If the concentration of H2S on activated carbon exceeds 3ppm, regeneration is required.
(2) iron oxide absorption process. The H2S in biogas is absorbed by ferric oxide. The desulfurization principle of this process is as follows:
Fe2O3? H2O+H2→Fe2S3? H2O+3H2O
(1) this reaction is exothermic, the minimum temperature is 12℃, and the optimal reaction temperature is 25℃ ~ 50℃. Therefore, in actual engineering operation, heating is required to reach the optimal reaction temperature. In addition, H2S removal is carried out by dissociating into H+ and S2+ in the water film on the surface of active iron oxide, and then carrying out chemical reaction. Because this reaction requires a certain amount of water, the moisture content of the desulfurizing agent is generally controlled at 10% ~ 15%. Therefore, the temperature of biogas in the previous dehydration process cannot be too low and the moisture cannot be removed too much, but the condensed water generated should also be avoided to make spherical iron oxide stick together, reducing the reaction surface and thus affecting the desulfurization effect.
Iron sulfide produced in the desulfurization process of this method can be oxidized and regenerated by air to produce iron oxide and elemental S .. The reaction principle of this process is as follows.
Fe2S3? H2O+3/2O2→Fe2O3+3S+609kJ
(2) As can be seen from the reaction formula, a large amount of heat will be released during regeneration, so spontaneous combustion often occurs. In order to prevent the desulfurizer from spontaneous combustion, it is generally necessary to spray a small amount of water on the discharged waste desulfurizer. In addition, after repeated use for many times, the surface of iron oxide will be covered with a layer of elemental sulfur, so it is necessary to replace iron oxide. Usually one unit is equipped with two reaction beds, one for desulfurization and the other for regeneration.
In the current biogas project of livestock and poultry farms, iron oxide absorption process is called dry desulfurization. In addition, there is a common wet desulfurization method. The desulfurizer for wet desulfurization is mostly sodium carbonate solution with concentration of 2% ~ 3%. The desulfurizer of both methods can be regenerated.
(3) biological desulfurization method. The method uses colorless sulfur bacteria, such as thiobacillus thiooxidans and thiobacillus ferrooxidans, to oxidize H2S into elemental S or H2SO3 under certain temperature, humidity and micro-oxygen conditions. The desulfurization mechanism is as follows: ①H2S gas dissolves, i.e. changes from gas phase to liquid phase; (2) Dissolved H2S is absorbed by microorganisms and transferred to microorganisms; (3) H2S entering microbial cells is decomposed, transformed and utilized by microorganisms as nutrients, thus achieving the purpose of H2S removal. The reaction equation is as follows:
2H2S+3O2→2H2SO3
2H2S+ O2→2S+2H2O
Most sulfur oxidizing bacteria belong to the genus Thiobacillus. Thiobacillus can be found everywhere, and inoculation is not required for H2S removal. In addition, most thiobacilli are autotrophic, and the surface of anaerobic digests can provide them with a micro aerobic environment and necessary nutrition for growth. Therefore, it is simple to apply biological desulfurization by directly introducing a certain amount of O2 or air into the anaerobic digestion tank or gas storage tank and keeping it for a certain period of time. Proper temperature, reaction time and air volume can reduce H2S content in biogas to 50ppm.
In actual application, the amount of O2 or air introduced into the biogas is determined according to the H2S content in the biogas, which is generally 2% ~ 6% air. For methane with different methane content, the explosion range in the air is different, so certain safety measures must be taken to prevent methane from introducing excessive air to cause explosion. At the same time, biological desulfurization also has the disadvantages that the process is not easy to control, the removed elemental S is easy to block the filler and damage the aeration, etc.
生物脱硫,沼气脱硫,
沼气提纯问题请点击了解。